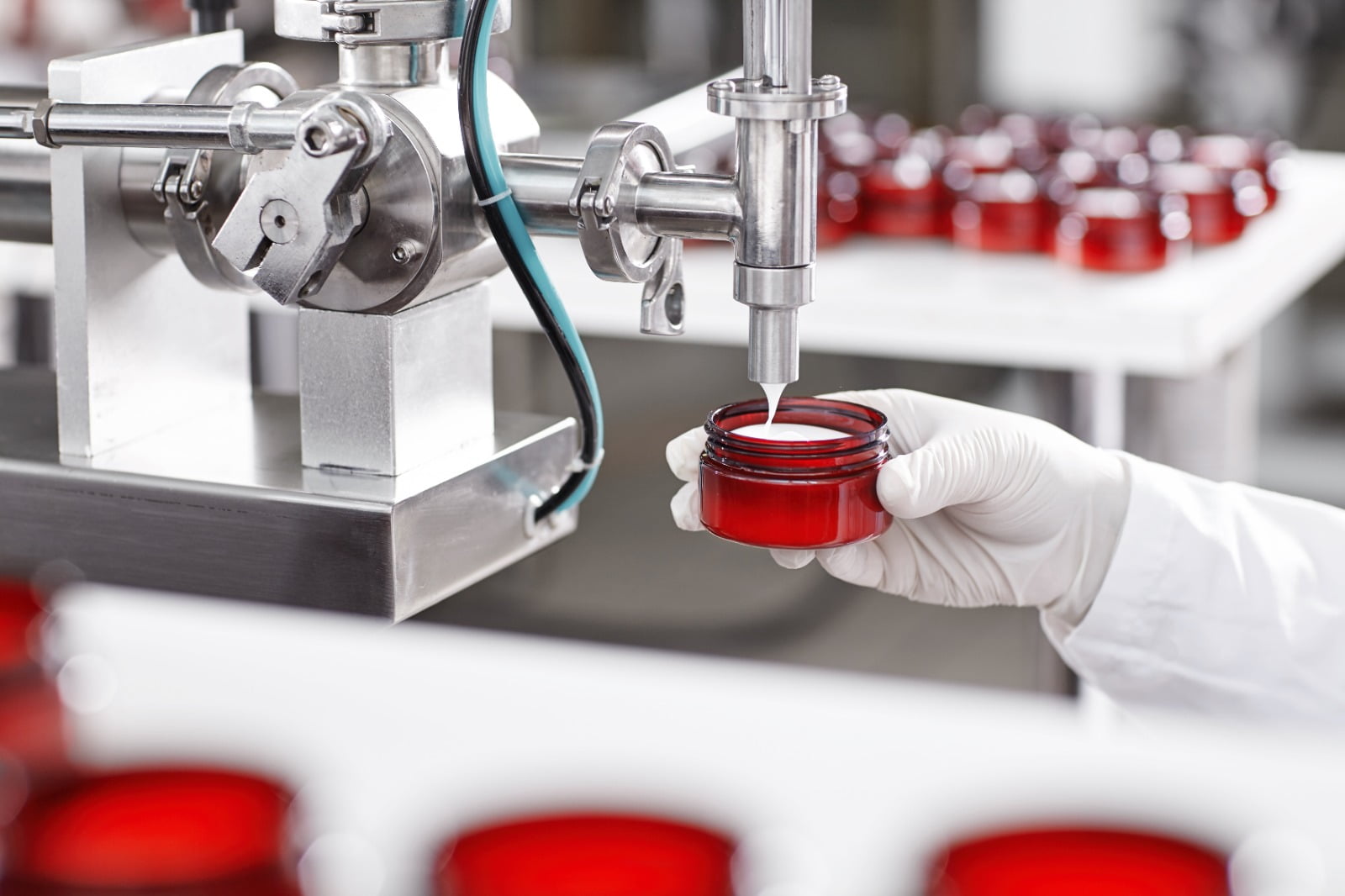
INTRODUCTION
Ointments are a crucial part of our everyday healthcare routines because they may treat a wide range of skin diseases. Nevertheless, have you ever wondered how these ointments are created? Chemistry, engineering, and quality control are all fascinatingly combined in the science of ointment production. We'll look at all of the complex steps that go into making ointments in this blog, from choosing the ingredients to packing them. Whether you're a seasoned pharmaceutical professional or just a curious consumer, this blog will provide you with deeper insights into all things related to ointment manufacturing plants.
Elements of Ointment Manufacturing:
The effective and reliable production of high-quality ointments requires ointment manufacturing equipment. This Ointment Manufacturing Plant is made up of multiple essential parts that cooperate to guarantee a productive production process
1. Water Phase Level:
A cylindrical tank with a jacket and spherically shaped dish ends is called a water phase vessel. There is a propeller-style stirrer available to mix the liquid.
2.Wax Phase Level:
The Wax Phase ( Sterile Vessel) is a cylindrical tank that is jacketed and has ends that resemble spheres. There is a propeller-style stirrer available to mix the oil or wax. Impurities are removed using a conical filter before the wax is moved to the manufacturing vessel.
3.Manufacturing Vessel:
The Manufacturing Vessel is a cylindrical, jacketed vessel with an anchor-style agitator and a conical bottom. The viscous result from the water and wax phase vessels is mixed with it.
4.Homogenizer:
The Homogenizer Tank is used with the manufacturing vessel to reduce particle size and promote uniform mixing.
5.Storage Vessel:
The Storage Vessel is a conical-bottomed tank, until it needs to be moved to the filling line. Depending on the needs, it can come with a jacket and an anchor-style stirrer.
6.Transfer Pump:
TheTransfer Pump is used to transfer a product from manufacturing vessel to the storage vessel.
7.Metering Pump:
This is a positive displacement pump through which a product can be delivered to the filling line at a regulated flow rate.
8.Interconnecting Pipeline:
In accordance with the layout, the plant has access to an interconnecting pipeline. Every pipe has an internal electropolishing.
9.Working Platform:
A suitable working platform to assist with plant maintenance and operation.
10.Control Panel:
The electrical control panel is where the controls and parts for the plant's operation are kept. It is possible to add specially designed automation to boost productivity and lower error rates.
Benefits of Ointment Manufacturing
Let’s now take a look at the vivid features of Ointment Manufacturing machines-
Precision
Machines used to make ointments provide unparalleled accuracy and consistency. Every batch of ointment produced is consistent in terms of composition and quality, guaranteeing that each product satisfies the exacting standards of the industry. In industries where product safety and efficacy are paramount, this degree of uniformity is essential.
Enhanced Production Speed
The speed of production is greatly increased by this equipment. The amount of time needed to mix, emulsify, and homogenize substances is decreased by automated procedures. In addition to meeting strong demand, this enhanced efficiency lowers production costs, which benefits customers by allowing for more affordable prices.
Hygiene
Additionally, ointment production equipment improves hygienic practices and reduces the possibility of contamination. These machine’s closed systems shield the manufactured ointments from outside impurities, guaranteeing their safety and purity. In pharmaceutical applications, where contamination might have devastating consequences, this is especially important.
Adaptability
Ultimately, these machines are a flexible tool for manufacturers due to their capacity to handle a wide range of compositions and batch sizes. Ointment manufacturing equipment gives manufacturers the freedom to adjust production to meet demand, whether they're making big quantities for mass distribution or tiny batches for specialized markets.
Conclusion
In conclusion, the adoption of ointment manufacturing machines brings remarkable benefits, including consistency, efficiency, hygiene, and versatility, making them indispensable in modern pharmaceutical and cosmetic manufacturing. For more information, visit Sterinox Systems (Pharmaceutical Equipment Manufacturer)